The Importance of Industrial Filtration
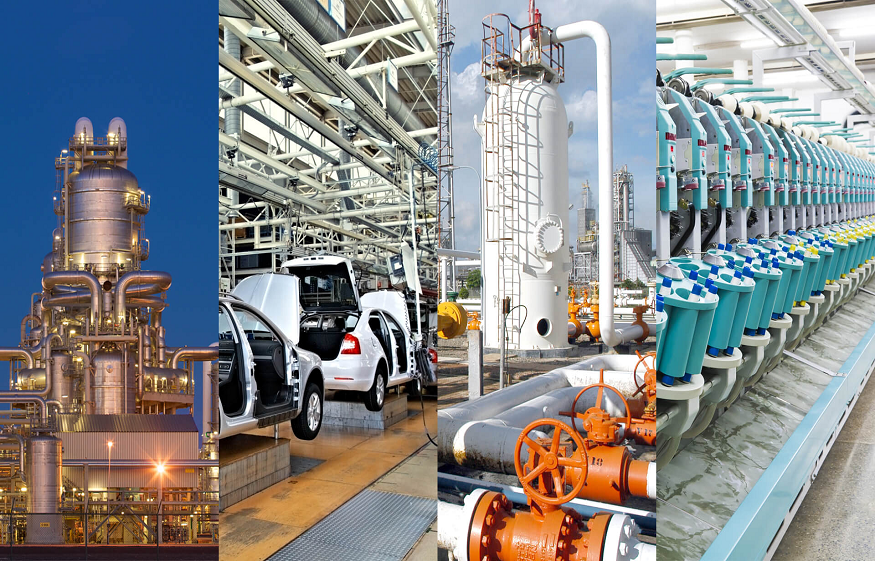
Filtration is used in electronics, chemicals, oil and gas, air and gas, food and drinks, and more. It’s for water, oil, chemicals, and coolants. Many companies filter materials during manufacture to maximize machine life.
In production contexts, industrial filtration systems gather pollutants to ensure product safety. Filtration systems protect process equipment and boost up time and performance. Manufacturers quickly acquire filtration equipment, proving its usefulness. As technology advances, better filtering equipment hits the market.
Industrial water filters.
In industrial uses, water filters remove pollutants. Small perforations in these filters let water through. Industrial water filtering technology is broad. Designed for industrial use. Industrial uses include reverse osmosis pre-treatment, nano and ultra filtration, UV sterilization, and ion exchange systems.
Bag filters
These filters provide continuous, high-speed filtration. It’s simpler and needs fewer accessories. These filters are cheaper than others.
Filters
Because they’re easy to replace, these industrial filters are used in many industries. Simple to maintain in industrial processes.
Auto-cleaning filters
This filter doesn’t need replacement. It’s compact and runs well without regular system modifications. Filters allow simple, one-time procedures. It provides efficient filtration and constant output.
Basket filters
Customizable filters with a greater filtration area. They capture particles during filtering. This makes it more bearable.
Cartridge filters and multi-media filters have unexpected uses.
In filtration, steel cartridge filters come in several sizes. These sophisticated filtration systems are built to last. Commercial water filters remove impurities, minerals, chemicals, sediments, particles, metals, and other pollutants. Various applications require different sorts of filters.
- Protecting equipment from contaminants. Production-related contaminants can damage machines. Industrial filtering captures and removes pollutants for proper removal and disposal. In pharmaceutical manufacturing, vacuum pumps eliminate moisture and transform a product into a powder.
- Decontaminating air and gas streams. Industrial filtration keeps air and gas clean during operations by removing contaminants. Complete and measured air and gas filtration removes unwanted contaminants. Many industrial operations require clean and pure outputs; little contamination levels can ruin products.
- Protect personnel and workplace. Air pollution can limit productivity. Better air quality increased worker productivity. Appropriate industrial filtration systems are crucial for equipment protection, personnel safety, and productivity.
Oil-lubricated vacuum pumps on the factory floor might emit oil mist. Under some conditions, an oil-sealed vacuum pump may release oil mist through the exhaust port, even with an OEM-supplied internal separator. This mist can generate unpleasant smells and make surfaces slippery, creating health dangers.
- Product separation from air stream. Many vacuum manufacturing processes demand high-efficiency solid-liquid-vapor separation. This improves system performance, captures process outputs, and reduces waste.
These specialized systems filter vapors, fluids, or solids from leftover production air. This is significant to some manufacturers. Essential oil manufacturers must isolate chemical ingredients under a vacuum to make a viable product.